Bio-Compounds
The arweco product lines at a glance
We offer you tailor-made compounds with different natural fibers, fiber content and biopolymer matrices. The name indicates which natural fiber has been incorporated into the compound. While Lignura® compounds contain wood fibers from domestic and PEFC-certified forestry, Otura® compounds contain untreated oat husks from organic cultivation.
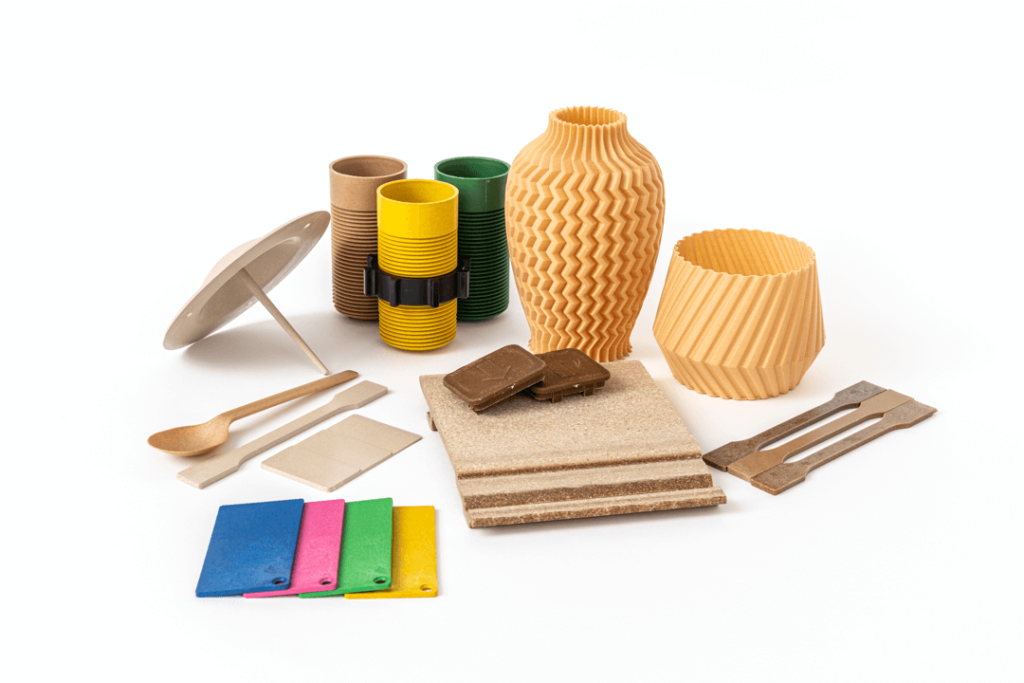
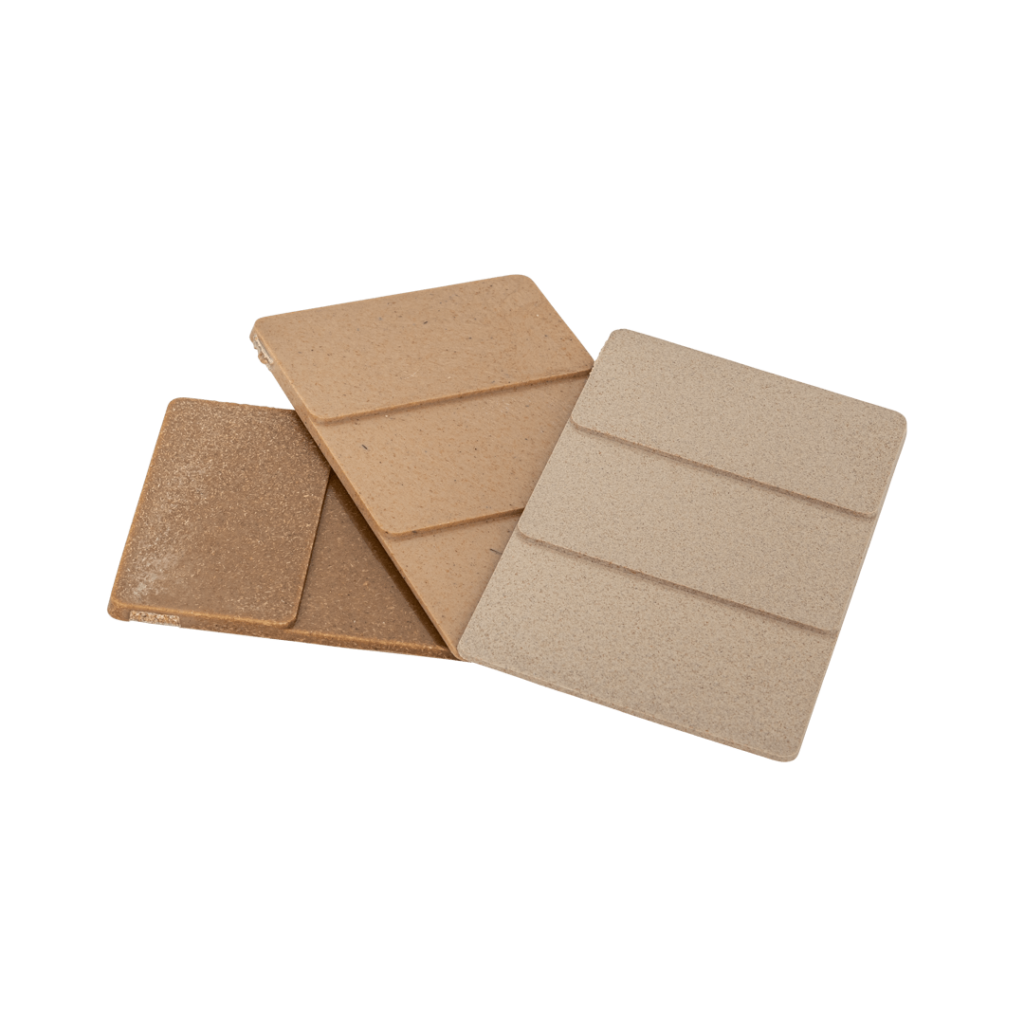
Biobased perfection:
Additives for process and product optimization
Depending on certain product requirements, different biopolymers with different fiber contents can be processed. The desired formulations can be customized. Depending on the requirements of the process or the product, biobased additives can also be compounded.
Natural Coloring:
Adaptability in further processing
The type and quantity of natural fiber used gives the compounds their natural coloring. Lignura® has more of a beige, woody tone, whereas Otura® appears a little lighter. We can also take color requests into account. Both product lines are easy to dye and have achieved brilliant color results. The desired coloring can also be realized during further processing of the compounds, e.g. in injection molding.
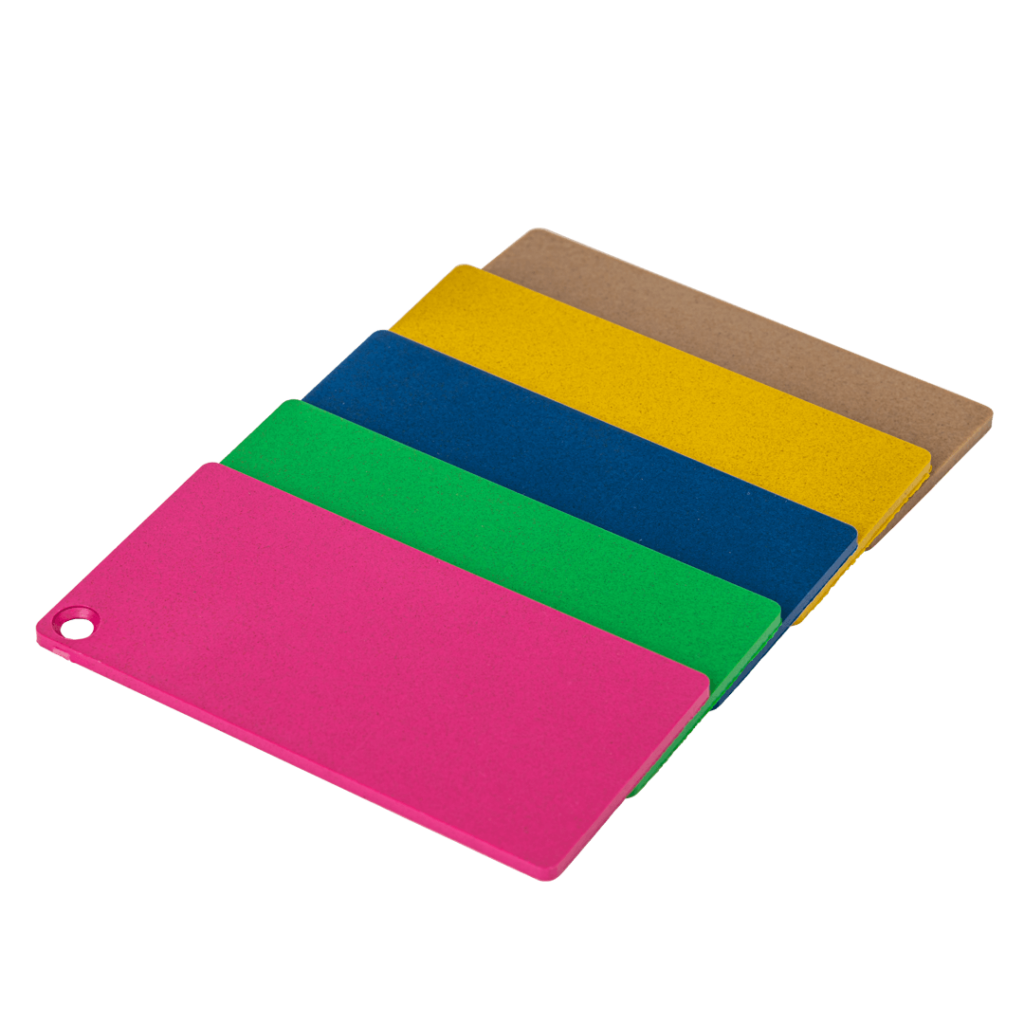
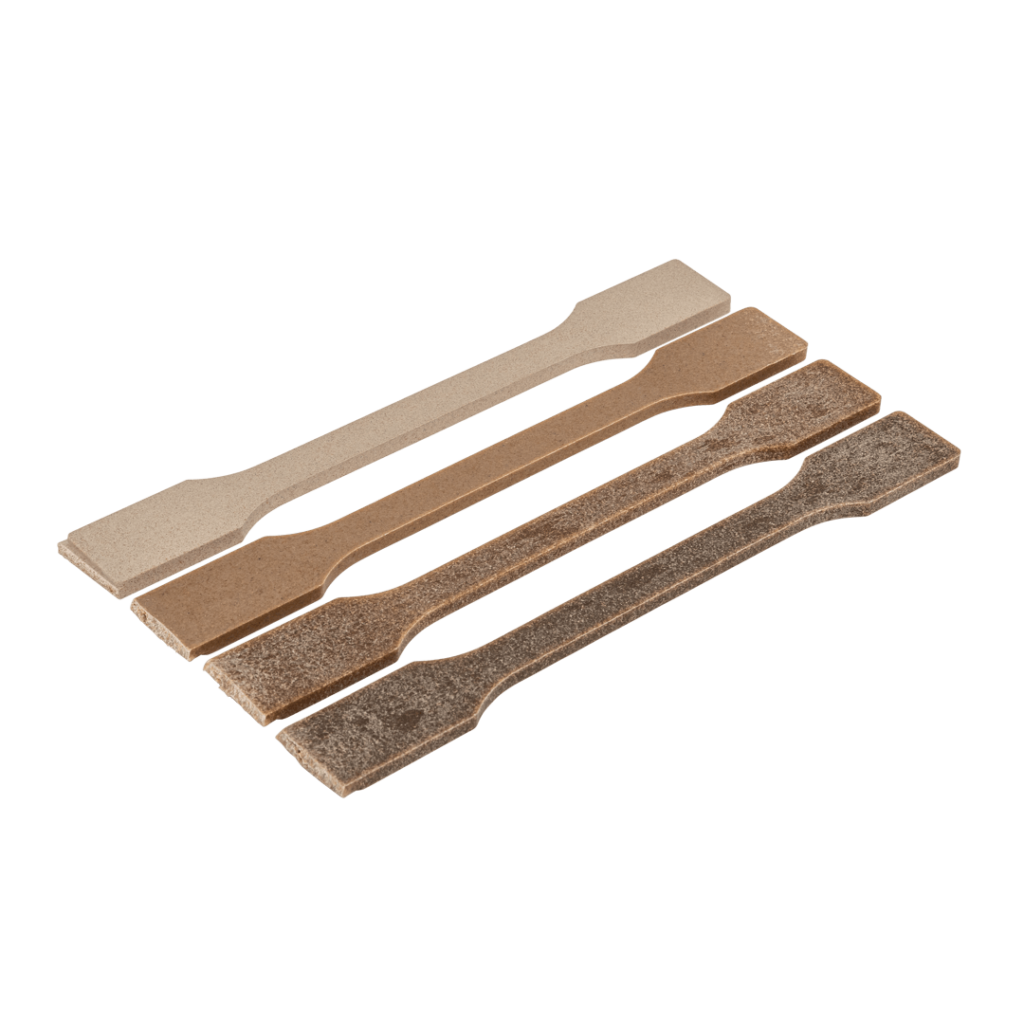
From stiff to flexible –
Product properties in comparison
The product properties vary depending on the choice of biopolymer matrix and fiber content. The desired properties and applications are determined by the choice of biopolymer matrix.
A reinforcing effect can be achieved by adding natural fibers. Within the biodegradable variants, degradability is improved with increasing fiber content. As the natural fibers are significantly cheaper than the bio-based polymers, our compounds are an interesting ecological and economical alternative to conventional plastics in terms of price due to the high incorporation rate of fibers. Of course, the incorporation of natural products means that natural fluctuations in product properties cannot be ruled out.
Mechanically, the two compounds differ slightly, while Lignura® compounds have somewhat more stiff, Otura® compounds are somewhat more flexible.
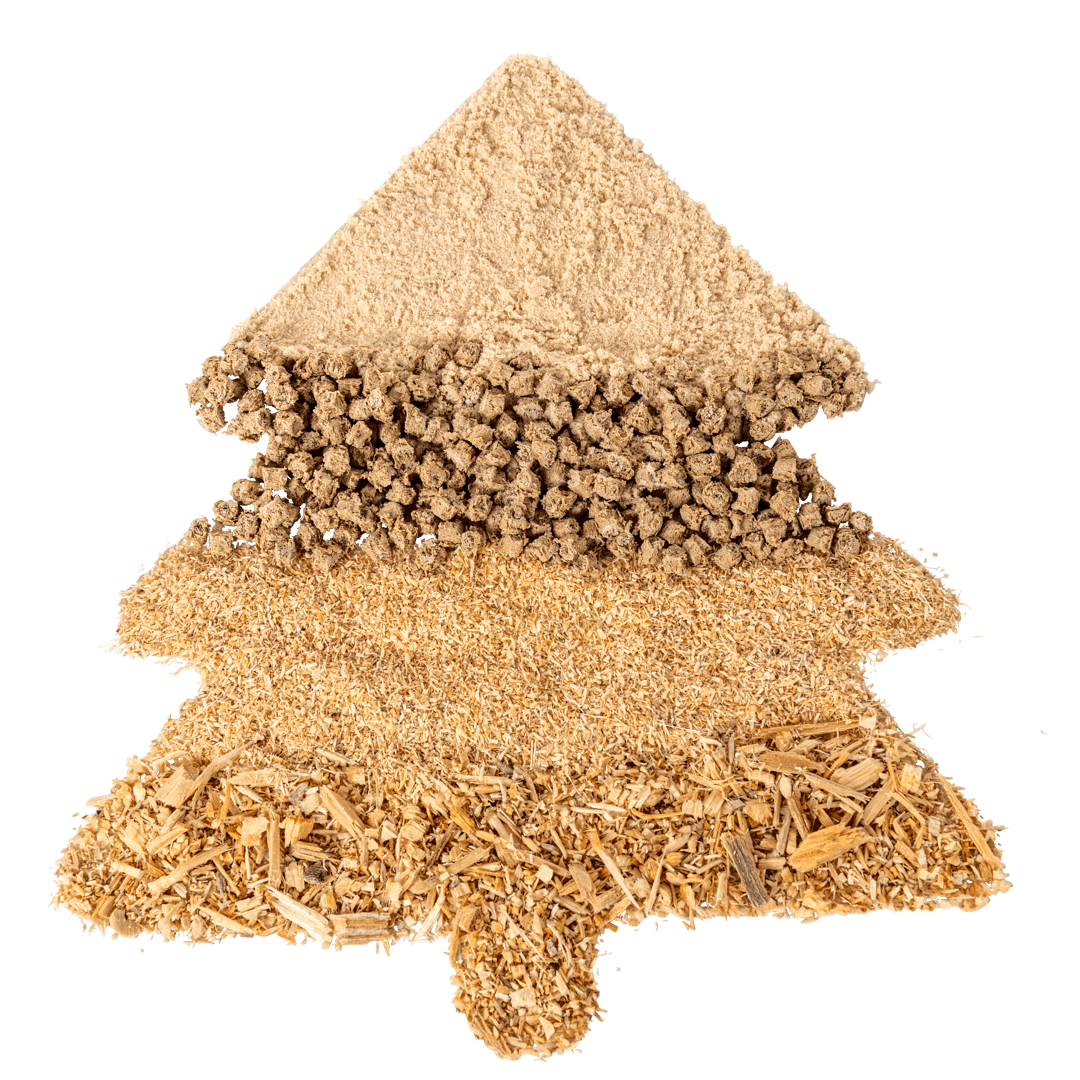
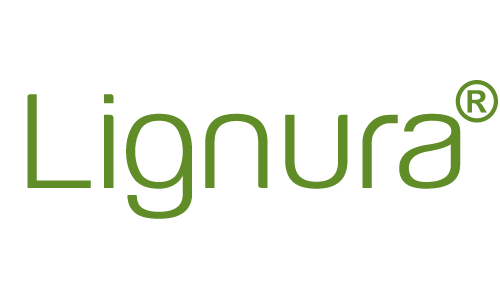
Lignura® stands for our wood fiber-based bio-compounds with different fiber contents and biopolymers
- wood fibers
- PEFC-certified
- sidestreams of the sawmill industry
- natural, woody color tone
- choice of recyclable, industrially compostable, home compostable and marine degradable biopolymers.
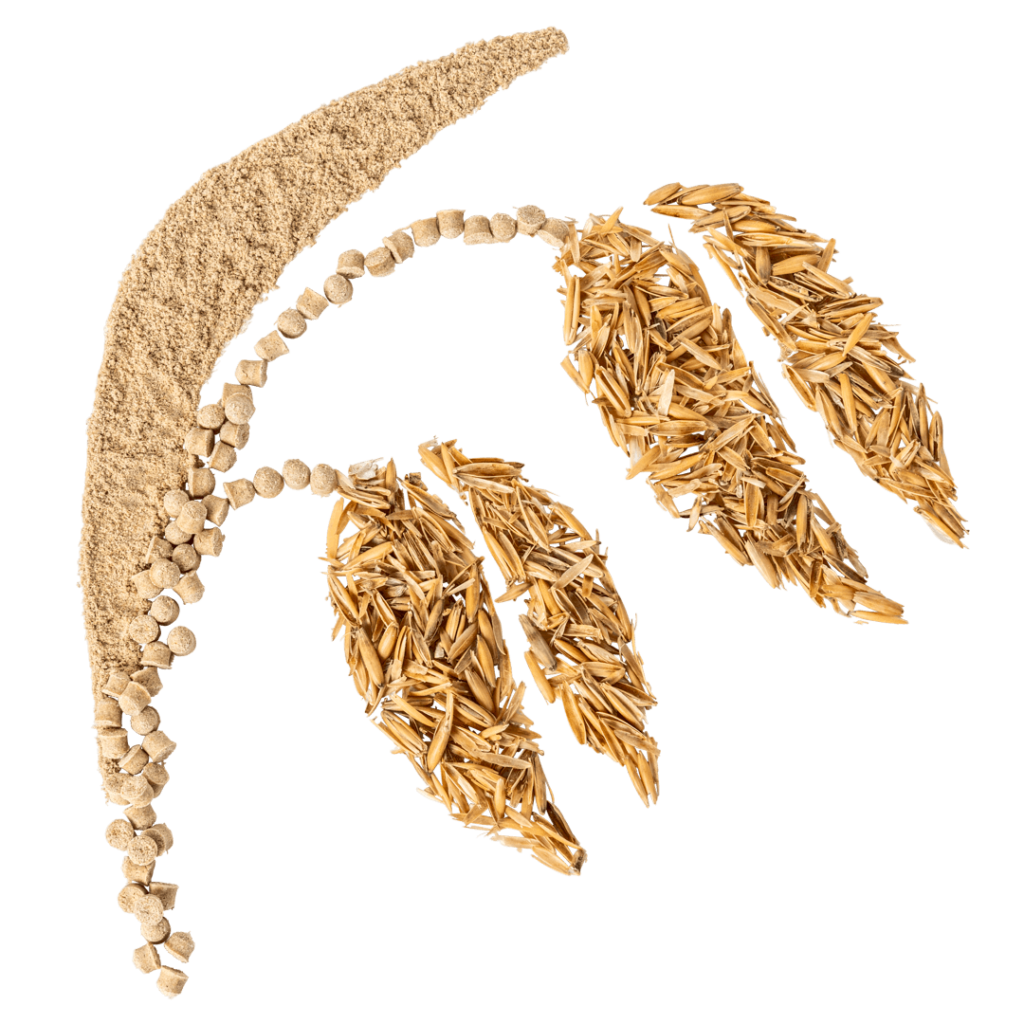
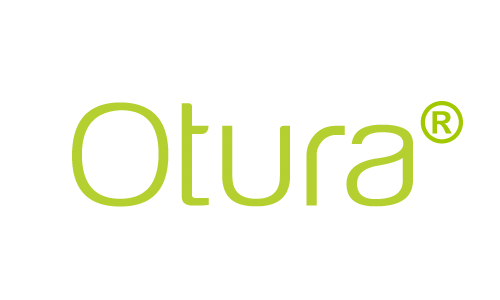
Otura® stands for our oat fiber-based bio-compounds with different fiber contents and biopolymers.
- fibers from oat hulls
- from organic cultivation
- sidestream from food inustry
- natural, beige color
- higher fiber content possible than with Lignura®
- choice of recyclable, industrially compostable, home compostable and marine degradable biopolymers
Your vision,
our know-how!
Any questions about how arweco bio-compounds can be used?
Contact us for individual support.
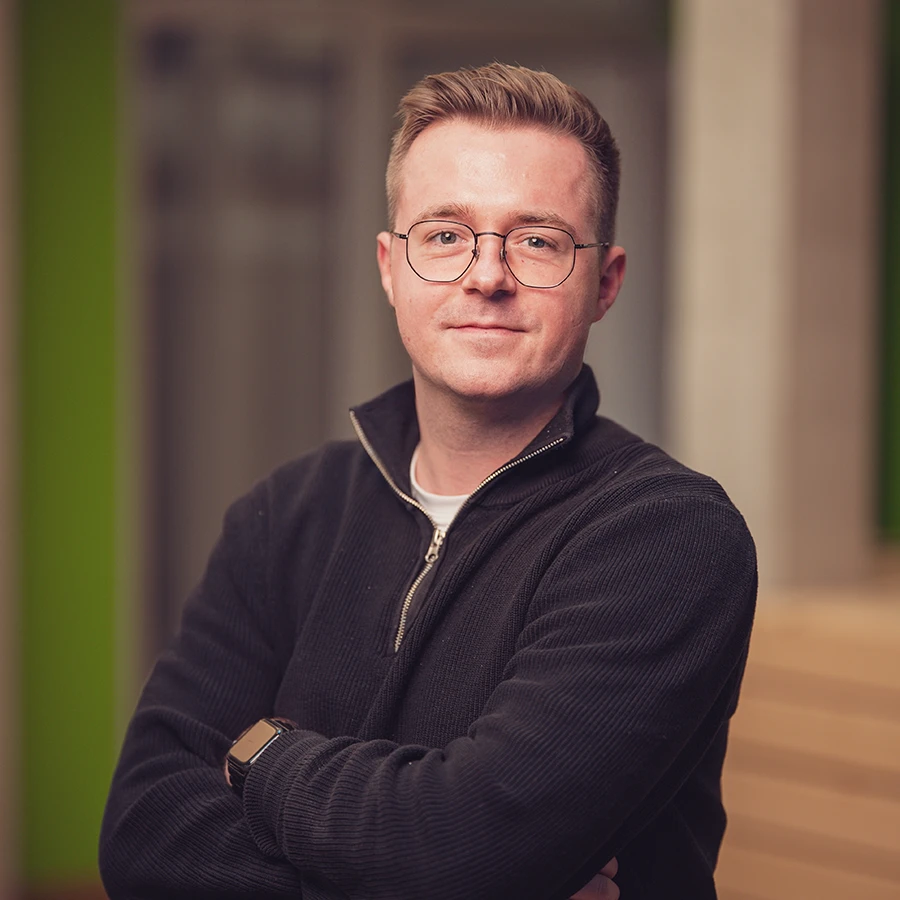
Processing advice
Natural fiber-filled compounds should always be processed as gently as possible. Processing instructions are therefore listed in the respective data sheets. Pre-drying for several hours between 60-70°C to < 1% moiture content is recommended in order to avoid undesirable effects during processing. High temperatures (>180°C) and extreme shear forces should be avoided.
Our bio-compounds are suitable for:
- Injection molding
- Extrusion
- Thermoformin
- 3D-Printing
Depending on the biopolymer matrix, we offer the following variants:
- biobased
- industrial compostable
- home compostable
- marine degradable
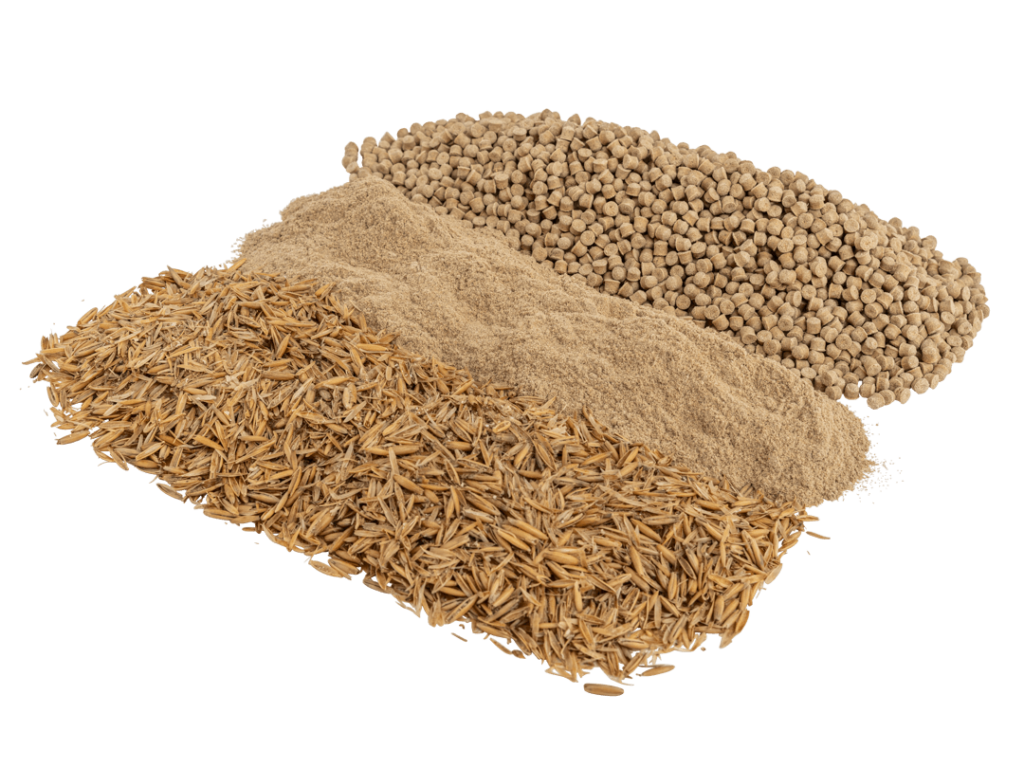
What differs Otura® from Lignura® and other products?
You can choose from bio-based and/or biodegradable biopolymers for recyclable, industrially compostable, home compostable or marine degradable applications. Use of renewable raw materials – this conserves finite petrochemical resources and the environment and reduces the CO2 footprint. The fine grinding and our patented processing methods result in a very uniform appearance through good particle distribution and a warm, natural color.
Ready for customized solutions?
With our R & D department, we can develop other variants for your product ideas customized to your process and application.
All advantages at a glance
- renewable raw materials from sidestreams of the food and wood industries
- residual materials that would otherwise have no material use
- PEFC/Ecological-Certification of wood/oat
- fiber content of up to 40 % possible with injection molding and up to 80% with extrusion
- natural color
- uniform distribution
- less abrasive than glass or carbon fibers
- choose from a large portfolio of biobased and/or biodegradable biopolymers for recyclable, industrially compostable, home compostable and marine degradable applications
- recyclability
- single-use or reusable use possible
- support in adapting to the individual process/product
- coloring possible
- reducing the CO2 footprint through renewable raw materials, local sourcing and processing
- reduced costs compared to pure biopolymers through the addition of fibers
- improvement of physical-mechanical properties (reinforcement)
- good processability for injection molding and extrusion